Gigantyczny kret dotarł na miejsce. Różne rodzaje transportu, miesiące przygotowań i tygodnie podróży. Jak zaplanować tak nietypową operację? Mówi o tym Tomasz Kwapis – Szef Przewozów Ponadgabarytowych w DB Schenker w Polsce, odpowiedzialny za transport TBM.
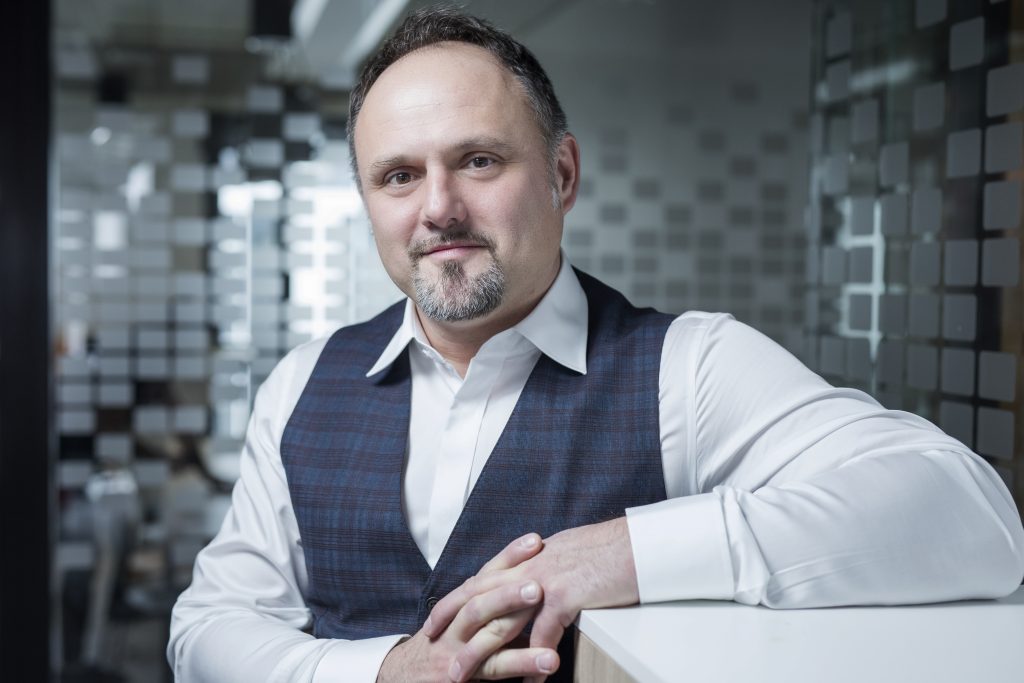
DB Schenker przeprowadził niedawno dużą, wieloetapową operację sprowadzenia do Polski maszyny TBM. Co to jest za maszyna i jakie jest jej przeznaczenie?
Nie jestem inżynierem, ani tym bardziej osobą projektującą czy wykorzystującą ten sprzęt. Jednak po prawie dwóch latach „znajomości” zdążyłem się dowiedzieć kilku ciekawych rzeczy o tym urządzeniu. Maszyny TBM (Tunnel Boring Machines), kolokwialnie nazywane „kretami”, służą do budowy wszelkiego rodzaju tuneli. Mogą to być stosunkowo niewielkie urządzenia do drążenia wąskich tuneli, np. do transportu bagaży miedzy terminalami w portach lotniczych. Drążą też nieco większe tunele metra. Są to też ogromne maszyny drążące tunele autostradowe – z taką mieliśmy właśnie do czynienia. Wyróżnia się dwie zasadnicze fazy jej pracy. Na początku tunel drąży przednia tarcza skrawająca. Czoło tarczy wyposażone jest w ostrza, noże oraz dyski tnące ze stali o wysokiej wytrzymałości. Urobek, za pomocą przenośnika ślimakowego, transportowany jest na taśmociągi i wywożony na zewnątrz. Druga, a zarazem ostatnia faza pracy tarczy TBM polega na układaniu obudowy. Po wydrążeniu odpowiedniej długości tunelu tarcza zatrzymuje się i uruchamia się hydrauliczny moduł układający pierścień tunelu. Następnie TBM powraca do etapu pierwszego i zaczyna drążyć dalej.
Maszyna po uruchomieniu nie zatrzymuje się – pracuje 24 godziny na dobę. Ciekawostką jest fakt, że urządzenia te często produkuje się specjalnie na potrzeby konkretnego projektu (chodzi przede wszystkim o średnicę tunelu). Zdarza się, że są to maszyny jednorazowego użytku, które po wydrążeniu tunelu już na zawsze zostają pod ziemią.
Korzystaliście z transportu drogowego, morskiego, rzecznego. Jak długo trwał sam okres przygotowawczy do tej operacji?
W kwietniu 2023 r. miną dwa lata od kiedy zaczęliśmy pracę nad tym projektem. Od początku wiadomo było, że najtrudniejsze będzie znalezienie odpowiedniego rozwiązania pozwalającego przetransportować TBM już po jej dotarciu do Polski. Proszę mnie źle nie zrozumieć. – Transport maszyny w Hiszpani, późniejsze operacje portowe, załadunek statku w Santander i, w kolejnych etapach, transport ze Szczecina barkami do Opola były dla nas, logistyków, czystą przyjemnością. Doświadczenie i odpowiednio dobrani partnerzy sprawili, że transport z Hiszpanii do Opola to, według mojej oceny, ok. 20% trudności całego projektu. Prawdziwym wyzwaniem było zaplanowanie i znalezienie rozwiązania na transport maszyny z Opola do Babicy. Ten etap zajął nam około roku.
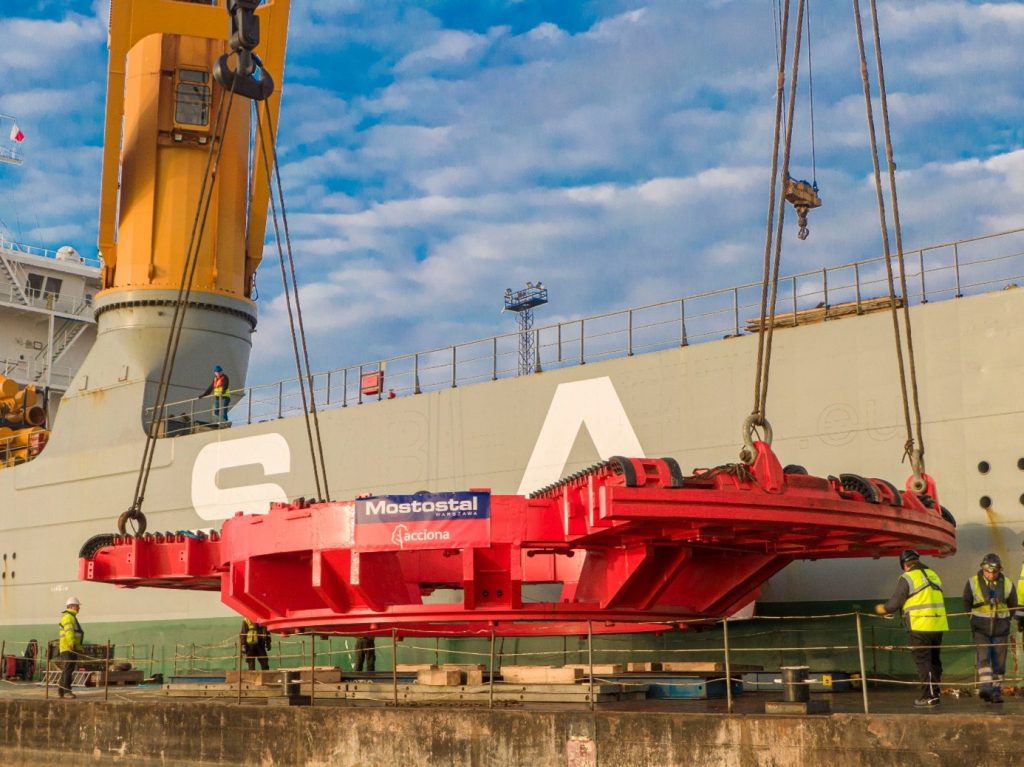
Zgranie w czasie tak wielu elementów to nie lada wyzwanie. Rozumiem, że wymagało to stworzenia i zaangażowania specjalnego zespołu?
Jeżeli ktoś zapytałby mnie, co stoi za sukcesem tego projektu, odpowiem, że są to właśnie ludzie, relacje i specjalistyczne know-how. Kluczem była wiedza jakich partnerów należało wybrać do realizacji poszczególnych etapów transportu.
Dzięki naszym kolegom z Hiszpanii zakontraktowaliśmy profesjonalnego i sprawnego lokalnego przewoźnika. Tak samo sytuacja wyglądała w przypadku wyboru portu w Santander i armatora morskiego, odpowiedzialnego za transport maszyny do Polski. W kolejnych etapach towarzyszył nam zespół z „naszego” portu w Szczecinie. Wspierała nas też wyspecjalizowana firma ze Szczecina, która zrealizowała przeładunek na barki i pontony oraz sam transport śródlądowy do Opola. Najważniejsze było jednak stworzenie zespołu, który odpowiadał za przygotowanie i realizację transportu drogowego do Babicy.
Jest to precedens w historii wielkogabarytowego transportu w Polsce. Przez cały czas trwania przygotowań trzon zespołu tworzyli pracownicy naszej firmy, przewoźnik, przedstawiciele klienta i administracji odpowiedzialnej za drogi w kraju. W międzyczasie załogę wspomagali także naukowcy z Politechniki Śląskiej i Rzeszowskiej oraz osoby odpowiedzialne za badanie mostów i projektowanie organizacji ruchu. To pokazuje, jak trudny i skomplikowany był ten transport. Mogę z cała pewnością powiedzieć, że dzięki takiemu podejściu i elastyczności zaangażowanych podmiotów udało się z sukcesem ten projekt wykonać.
Co stanowiło największe wyzwanie w tej operacji? Który z etapów był najtrudniejszy, najbardziej czasochłonny?
Jak wspominałem wcześniej, najtrudniejszy był etap transportu maszyny już na terenie Polski. W momencie planowania, rozwiązując jeden problem z maksymalnym dopuszczalnym przez polskie prawo naciskiem na osie (11,5 tony), stworzyliśmy kolejny. Byłaby nim ponadwymiarowa długość zestawu. To natomiast spowodowałoby wzrost masy całkowitej oraz brak możliwości pokonania większości zakrętów. Do tego dochodziła jeszcze kwestia rozłożenia masy ładunku na całym zestawie. Powierzchnia nacisku to ok. pięć metrów, a zestaw miałby już prawie 100 metrów długości. Nie ma takiego sprzętu (osi), który gwarantowałby właściwe rozłożenie ciężaru na tak długiej platformie. Szukając kolejnych rozwiązań, doszliśmy do konfiguracji zestawu ważącego ponad 600 ton. Absolutnie zamknęloby nam to praktycznie wszelkie możliwe drogi transportu, za sprawą niewystarczającej nośności mostów na trasie.
Musieliśmy znaleźć takie rozwiązanie, które spełniłoby wszystkie wymagania, a zarazem nie powodowało wzrostu masy całkowitej zestawu. Udało nam się do projektu zaangażować jednego z wiodących producentów naczep i sprzętu do przeprowadzania tego typu transportów w Europie. To właśnie ta firma podsunęła nam pomysł. Później, na nasze zlecenie, zaprojektowała i wyprodukowała specjalnie na potrzeby tego transportu elementy spajające kładki (fly over bridge) z elementami naczepy. Służą one zwykle do wzmacniania mostów na czas przejazdu ciężkich ładunków. W efekcie udało się stworzyć zestaw transportowy, jakiego jeszcze nikt nie widział. Most łączący dwie platformy jezdne, posiadające po 17 osi każda. Jest położony na specjalnych obrotnicach, zespolony z wyprodukowanymi na potrzeby tego projektu elementami. Innowacyjne było właśnie wykorzystanie nakładek na mosty jako elementów nośnych zestawu transportowego. Uff… Ciężko to opisać tak, aby było klarowne i zrozumiałe.
Gdy już skonfigurowaliśmy zestaw, wystarczyło „tylko” znaleźć odpowiednią trasę dla takiego transportu. To zajęło nam kolejne miesiące żmudnej pracy.
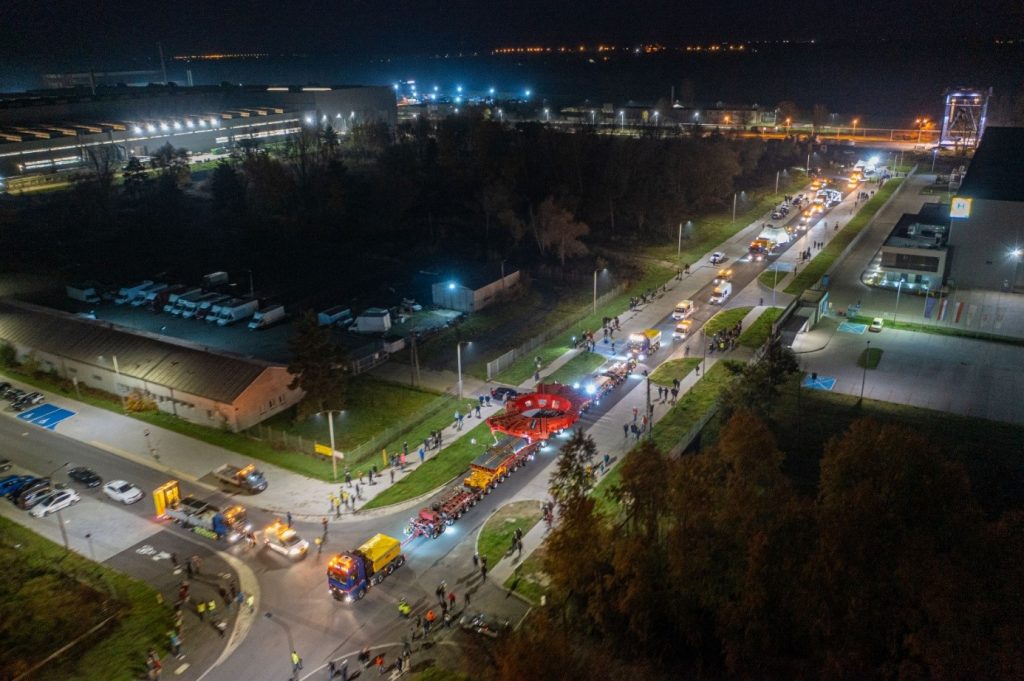
Takie zadania, jak sprowadzenie ponadgabarytowego towaru, to wyjątkowa sytuacja dla DB Schenker? Jak często stajecie przed takimi logistycznymi wyzwaniami?
Transport ponadgabarytowy, czy jedynie drogowy, czy w połączeniu z czarterem statków, jest dla nas praktycznie codziennością. Oczywiście, kilkukrotnie zdarzyło nam się już realizować bardzo trudne i skomplikowane projekty. Odpowiadaliśmy np. za przeniesienie całej linii produkcyjnej ze Szwecji do Polski czy transport elementów na potrzeby rozbudowy rafinerii. Tak złożonego projektu jak TBM jeszcze jednak nie realizowaliśmy. Słusznie mówi się o transporcie, jakiego w Polsce jeszcze nie było.
Wywiad powstał dla czasopisma Logistyka a Jakość.